Automotive & Transportation
Metal Working Additives: We provide a variety of chemicals used in lubricant intermediates to produce additives as well as final components to improve lubricant performance in base oils and metal working fluids.
Refinery Applications
TBPS 454 is a sulfiding agent, which is used along with a reducing agent such as hydrogen, to transform metal oxide species to a metallic sulfide crystalline phase in situ for hydrotreating catalysts. For in situ sulfiding, the reaction is performed inside the process unit for complete control and to achieve maximum catalyst activity and safe handling.
Advantages
Unlike other sulfiding agents, TBPS 454 is not classified as a flammable material. It also has a low toxicity rating. TBPS 454 has a diesel-like odor, a more friendly and common smell for refineries. TBPS 454 also starts to convert to H2S at the lowest temperature compared to other sulfiding agents, lowering the risk of reduction of metals and potentially lessening the time of the sulfiding operation. The hydrocarbon byproduct during a sulfiding operation for TBPS454 is isobutane, which does not have the potential to dilute hydrogen in the recycle gas during a sulfiding operation.
Packaging
TBPS 454 is available in bulk (tank trucks and ISO containers) or packaged containers including 250 gallon plastic totes and 54 gallon drums.
Safety and Handling
TBPS 454 is an environmentally hazardous substance and a marine pollutant. It also has a high viscosity rating, making it difficult to handle during cold weather. It is not soluble with water but is soluble in hexane and white spirits. TBPS is compatible with both carbon and stainless steel. Teflon or Viton gaskets are recommended for the injection of TBPS 454.
There are no known incompatible materials. Household bleach (not pure bleach) or Liquid Alive® bacteria is suggested for any needed clean up. Please reference the MSDS for additional handling and safety recommendations.
Comparison of Other Polysulfides
TBPS 454 is di-tertiary butyl polysulfide, a mixture with a predominance of tetra and penta sulfides. It is not a distilled material. It is the highest sulfur content polysulfide manufactured. Other polysulfides available are TNPS 537, TDPS 532, and TDPS 320. These products are utilized in the metalworking lubricant markets.
Performance Data
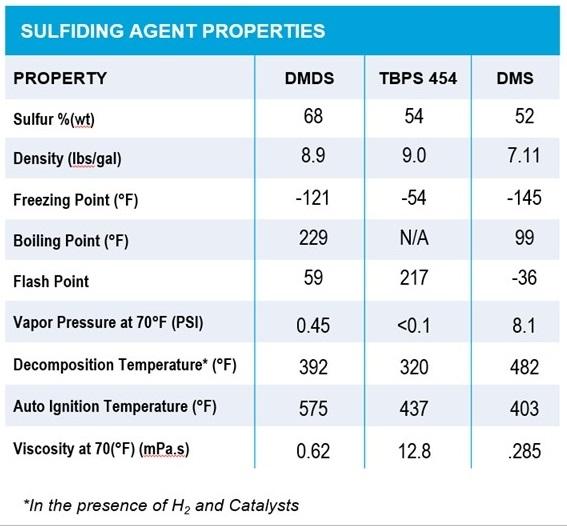
Application Guidelines
For in situ sulfiding of hydrotreating catalysts, the catalysts will typically be dried and then wetted with feed material at 300°F or below. TBPS 454 injection begins as the temperature approaches 400°F, with the reactor held in a range of 400–420°F until H2S breakthrough occurs. Breakthrough is indicated when the H2S level of the recycle gas exceeds 5000 ppm. The reactor temperature can then be raised to the secondary sulfiding plateau, which is typically in the range of 620–670°F. The temperature will be held at this level for at least 4 hours until the sulfiding process is complete. A secondary H2S breakthrough may occur at this point, with H2S levels rapidly exceeding 20,000 ppm (see figure below).
Typical Feed Sulfiding Procedure
TBPS 454 decomposition can form elemental sulfur. Elemental sulfur with the combination of olefins can create a solid polymeric product. This risk increases with an excess of TBPS 454 injected during a sulfiding operation at temperatures below 500°F. The injection point needs to be as close as possible to the catalyst bed to avoid potential deposits in the preheating section which can leave solid deposits in the piping and on the catalyst. Gas phase sulfiding is not possible in order to avoid any solid formation. TBPS 454 also breaks down to Tertiary Butyl Mercaptan, a high odor chemical. (See figure below).
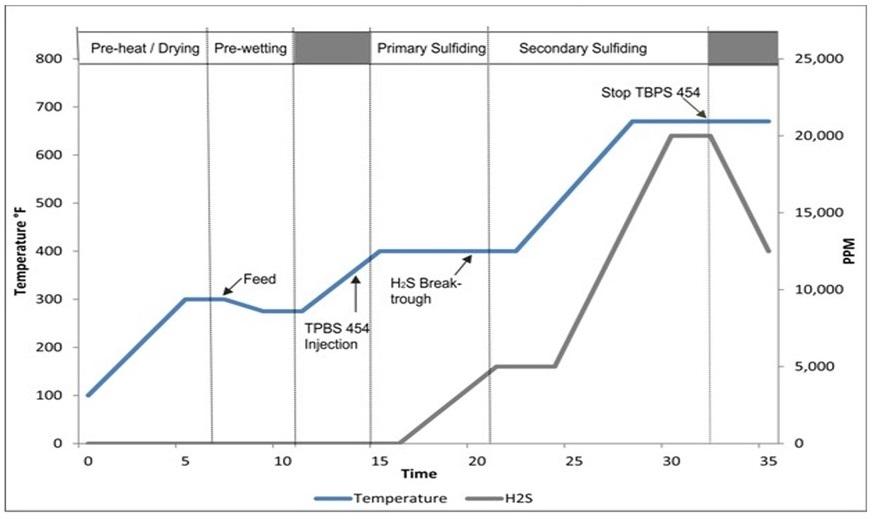
Decomposition of TBPS 454 in the Presence of a Catalyst
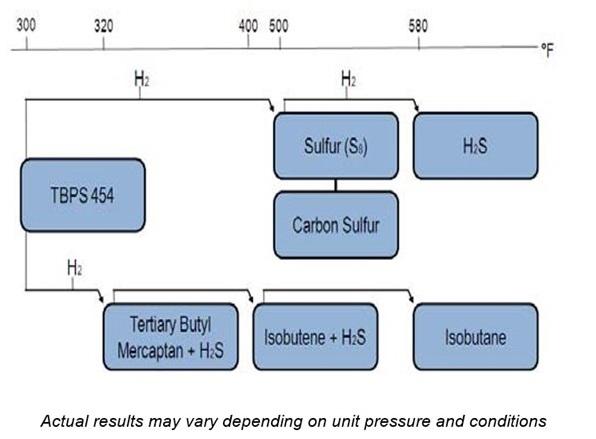