The addition of maleic anhydride to a normal alpha olefin generates an alkenyl succinic anhydride (ASA) that can be an entry point to several polar derivatives. Some ASAs are available commercially; alternatively, the addition is easily performed in a batch reactor and the ASA is separated from unreacted olefin by distillation. No solvent or catalyst is necessary, and the technology can be practiced with our entire range of normal alpha olefins from 1-butene to C30+ normal alpha olefin wax.
The typical reactions of organic acid anhydrides with water, alcohols, amines and metal hydroxides can be used to generate numerous derivatives such as alkenyl succinic acids, half-esters, diesters, succinamic acids, succinamides, succinimides and ASA salts, some of which are shown below.
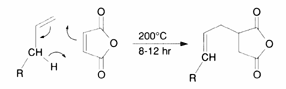
Polyfunctional reagents such as polyamines and polyhydridic alcohols can be used to generate polyamides and polyesters. Many of these derivatives have surface active properties and can be used as emulsifiers, thickeners, dispersants, surface modifiers for leather, textiles, and paper, and corrosion inhibitors.
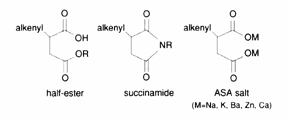